Buy American Quality at Premium Chinese Prices
By Wei Chen
April 22, 2008
"American Factory in Chinese Land" |
"Today's economy is truly global and the scaffold industry is an active participant,"said John Miller, the President of Scaffold Industrial Association. Thanks to the globalization in the world economy, the scaffold has become a global commodity. According to the data from International Trade Administration of U.S. Department of Commerce, U.S.? imported over $77 million worth of scaffolding products from 34 countries in 1999 and the largest trading partner was Canada at $21.5 million. Not surprisingly, U.S. has imported over $269 million worth of scaffolding products from 41 countries in 2006, the largest trading partner was China at $134 million. The total imports from the world have more than tripled in 7 years and the total import from China has increased from $8.9 million in 1999 to $134 million in 2006, over 1500% growth. 2007 is another record year as it has already reached $260 million from the worldwide and $125.8 million from China as of November 2007.
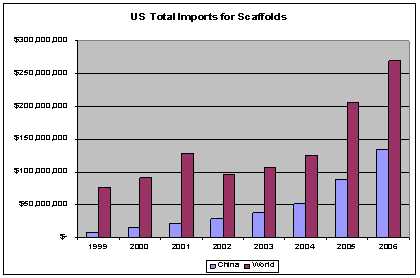
Figure 1: Total Import for Scaffold by U.S.
The global competition is good and healthy for the scaffold industry. For many years, a few US manufacturers have dominated the market place and the purchase cost of scaffolds has stayed high due to the lack of availability. As the scaffold has become a global commodity and is getting more and more affordable, it has stimulated the growth of the scaffold industry. More and more applications have used scaffolds where they were not cost effective in the past. More and more contractors started to carry the inventory for scaffolds as it becomes more affordable to buy in stead of rent. Many scaffold rental companies are able to grow vigorously as their growth is not limited by the availability of scaffolds any more.
Unfortunately, not all scaffolds are made at the same quality and meet the same standards. There are over 200 scaffold manufacturers in China. Most of them locate in Wuxi area, Jiangshu province, and one hour driving distance from Shanghai. Due to the low labor costs and inexpensive equipment investment, a Chinese factory can start manufacturing scaffolds with as little as $10,000 investment and less than 10 workers. As Chinese domestic market demands low cost scaffolds in place of bamboo scaffolding and steel pipe scaffolding, the majority of factories in China manufacture scaffolds at the quality level far below American standards. While these factories are manufacturing scaffolds and compete in the Chinese market, they are also aggressively seeking the opportunities to export scaffolds to the developed countries like the U.S. and Canada.
Here comes the danger! When the inexperienced buyers purchase the scaffolds from these Chinese factories, they inherit huge risk and liability for substandard scaffolds. They don¡¯t get the second chance when poorly fabricated scaffolds collapse before it becomes overloaded. It is even more dangerous if they purchased the scaffolds from Chinese factories directly or merely through a trading agent/broker who is without vested interests and recourse. One accident can send the company to the bankruptcy court and the negligent persons to jail! Buyer Beware!!
How much scaffold is "Made in America"?
The cost difference is the main reason to drive the growth of imported scaffolds. So why is there such a huge cost difference? Of course, the labor cost in China is so low. But is that the only reason? Not necessarily! Let¡¯s take an example of manufacturing a 5-foot-wide walkthrough frame.
A good welder in China earns $300 to $500 per month while the salary for a well-paid welder in the US is around $2500 to $3000 per month. The difference is obvious! However, labor cost is not a big percentage of the total cost for making a piece of scaffold. Each welder can weld 70 pieces of 5 foot-wide walkthrough frame in 8 working hours. So the average welding cost is $0.20 per frame in China and $1.60 in the US. The rest of the manufacturing cost is about the same, like steel raw material, cutting and punching process, and powder coating, etc. as these processes are highly automated in the US and do not utilize a lot of labor. But, the ocean freight cost is about $0.10 per LB to ship from China to the US in a full 40 foot container. Each 5 foot-wide walkthrough frame weights about 48 LBS. Therefore it costs about $4.80 per frame to ship each frame from China to the US east coast! Compared with the freight cost, the saving on the manufacturing process is not significant!
But, why are the scaffolds "Made in America" so much more expensive? Overhead and higher margin! The operating overhead in the US is significantly higher than that in China! In addition, the U.S. scaffold manufacturers demand higher margin because the higher overhead required in having a U.S. based operation, also because their products are claimed as ¡°Made in America;¡± therefore it is perceived higher value. The factories in China who sells directly, or the broker/agent who is usually a one man operation, can survive with lower margins because they do not have a U.S. based operation and do not have to cover the U.S. overhead.
"American Factories in Chinese Land"
Recently the quality of the scaffolds made in China has been brought into spotlight and Chinese scaffolding manufacturers are being criticized as inferior manufacturers. Even though we agree that there are a lot of Chinese manufacturers who do not currently make products that meet North American and international standards, we also need to recognize that China, as a country who has successfully put a space shuttle into the orbit in the last year, certainly has the ability to make as good scaffold as any country. There are Chinese manufacturers who do understand the North American and international standards, employs well trained and intelligent workers, and depends on a stringent quality assurance system to control its product quality. ?We call such factories as "American Factories in Chinese Land" who is able to make high quality scaffolding meeting and exceeding the quality made in America.
So how can we distinguish "American Factories in Chinese Land" from ordinary Chinese factories? After visiting more than 100 Chinese factories in the last ten years, our experience has helped us define our qualification criteria for "American Factories in Chinese Land."(AFCL)
1. Working Environment
"AFCL" provides CLEAN, SAFE, and COMFORTABLE working environment for its employees and workers. Their workers are happy and enjoy working in the factories and their work stations are clean and safe. The workers are paid well, considering the cost of living in China. The salary ranges from $200 to $500 per month, but this salary can support their family and provide the education for their children. A happy, willing and proud workforce is essential to manufacture quality products consistently.
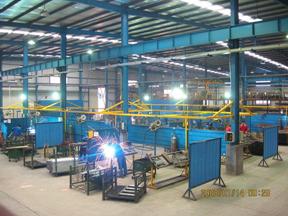
Figure 2: Overview of Factory Floor Figure 3: Overview of the Automated Powder Coating Line
2. Understanding the products and standards
What am I making? How will the products be used? What are the safety requirements? As part of manufacturing process, an "AFCL" invests in understanding the products and the North American and international standards for material strength, welding methods, and loading requirements putting forth by organizations like ANSI, OSHA, AWS and etc., before manufacturing a single product for that market.
As simple as the scaffolding is to make, people's lives depend on how well it is made. That¡¯s why there are minimum safety standards that simply can not and should not be ignored. It is dangerous for a manufacturer to simply start making scaffolds without understanding the safety standards. Unfortunately higher market demand has lured many Chinese factories plunging into this industry with the focus on making the scaffoldings as cheaply as possible. That focus is definitely misplaced and could have deadly ramifications.
The "AFCL" has the understanding to make the products that meet and exceed the safety standards that are defined in ANSI and OSHA regulations first, then try and find efficiencies in the manufacturing process to lower cost; thereby achieving the best quality/price ratio in the market place.
3. Raw Material Selection
The tensile strength, yield strength, and elongation are three critical requirements for the strength of steel tubing used in the manufacture of scaffolds. According to ASTM and ANSI standards, the hot-roll steel tube used on scaffolds shall have minimum yield strength of 50,000 psi and minimum tensile strength of 70,000 psi. The elongation requirement is 20% minimum. Chinese Steel Q235 falls below these requirements. However, Chinese Steel Standard Q345 or Q390 are far exceeding these requirements. Q345 has the minimum yield strength of 63,000 psi and the minimum tensile strength of 75,000 psi. And Q390 has the minimum yield strength 73,000 and tensile strength of 83,000 psi. Both elongations exceeds 20% minimum. While there are growing concerns on the quality of steel tubing being manufactured in China, a few large steel mills can manufacture the highest quality steel coil meeting and exceeding all the requirements. "AFCL" only uses steel tubing manufactured by these approved steel mills to guarantee the consistent quality of the steel tubing. The raw material shall be checked and tested during the Incoming Material and Components Check and is documented.
The weld seam in the tubing is also a critical point for the quality of steel tubing. There are multiple tests, such as the Flattening and Flaring testing, to check the quality of the weld seam of the steel tubing. "AFCL" performs these testing for each Heat number of steel coil. Also it is important to trace each Heat Number throughout the production process. We will discuss the Traceability later.
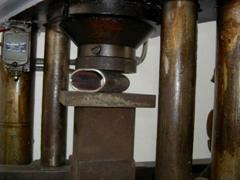
Figure 4: Tube Flatting Test Figure 5: Tube Flaring Test
Similar to the steel tubing, there are concerns of substandard components being used on the manufacture of scaffolds. We know some American factories do purchase some of their components from Chinese vendors. It is only a matter of selecting the good vendors for quality components. "AFCL" only uses the components manufactured by the vendors approved by AFCL¡¯s customers. These vendors shall be assigned a Vendor ID and imprint the ID on each component if practical! The components should also be checked during Income Material and Components Check.
4. Welding
"AFCL" fully understands AWS D1.1 and D1.3 standards established by American Welding Society (AWS). They provide ample training for all new welders and certify all the welders before they can weld on the production line. All the training and certification are documented for the record and inspection. Equally important, they don¡¯t allow each welder to weld more than 8 hours a day without necessary rest between shifts.
However, the certified welders cannot weld well without proper tools and equipments. "AFCL" provides the best equipment, such as the UK made OTC welding machines and welding mask with flash lens, to its welder. The cost of better equipment is more expensive but it is worthwhile as it guarantees the proper welding fusion. In addition, good welding fixtures are essential to the good welding quality: 1) The welding fixture needs to be at the waist height in order for the welders to weld efficiently and not to get tired easily; 2) the "smart" fixture will detect the quality problem for semi-finished raw materials: if the components and steel tube cannot fit into the fixture, it indicates there is a potential quality problem; 3) The welding fixture will fix each component tightly to avoid distortion during weld heating process.
"AFCL" also consistently checks the welding quality during the manufacturing process. Nothing will pass to the next station until it is checked and authorized by Quality Control Team. Any issues found and corrected are also documented for future references!
|